۱- جوشکاری پلاسما
وقتی که یک گاز تا چندین هزار درجه سانتیگراد گرم شود، اتمهای گازی به صورت یونهای مثبت و الکترون تجزیه میشوند و گاز به صورت یک هادی الکتریکی در میآید. این تغییر حالت را پلاسما مینامند. در فرآیند PAW نیز از این خاصیت استفاده شده است. بدین صورت که ابتدا با انرژی قوس گاز به یونهای مثبت و الکترون تجزیه میشود. سپس با ترکیب مجدد این یونها، اتمهای خنثی تولید شده و انرژی خود را به صورت حرارت از دست میدهند. در فرآیند PAW از دو نوع گاز استفاده میشود. یک گاز به عنوان پلاسما و دیگری به عنوان گاز محافظ بهکار میرود. قوس مصرفی نیز به دو صورت ممکن است ایجاد شود. یک قوس بین الکترود و لوله اوریفیس ایجاد شده که موجب گرم شدن گاز پلاسما میگردد. وقتی که گاز پلاسما از اریفیس خارج شد، به یک گازخنثی تبدیل میشود و انرژی خود را به صورت حرارت از دست میدهد. این حالت را قوس غیرانتقالی مینامند. در صورتی که قوسی از الکترود تنگستن به قطعه کار منتقل شود، قوس انتقالی ایجاد میشود. روش قوس غیر انتقالی برای اسپری پلاسما و روش قوس انتقالی برای جوشکاری استفاده میگردد.
گاز محافظ مورد نیاز از اطرف بدنه اوریفیس، قوس و حوضچه جوش محافظت میکند. این فرآیند شباهت زیادی به فرآیند GTAW دارد، با این تفاوت که در این فرآیند قوس تولید شده، توسط دریچه اریفیس منقبض شده و گرمای بیشتری نسبت به GTAW تولید میکند. اگر در هر دو فرآیند PAW و GTAW از یک جریان استفاده شود، در فرآیند PAW حرارت بیشتری تولید می شود و سرعت جوشکاری نسبت به GTAW بیشتر خواهد بود، زیرا در این فرآیند قوس منقبض می شود. در نتیجه از این روش به خـاطر استفاده از جـریان کم برای حـرارت زیاد، جهت جوشکاری فلزات نازک استفاده میشود. رویه دیگر جوشکاری با پلاسما سوراخ کلید نام دارد. در این حالت خاصیت نیروی کشش سطحی، فلز مذاب را به حالت اول برگردانده و جوش را ایجاد میکند. بدین ترتیب فلزات بسیار ضخیم در یک پاس جوشکاری میشوند. بسته به نوع جنس این ضخامت تغییر میکند. مثلا درمورد آلومینیوم این ضخامت ۱۹ میلیمتر است.
در این روش قوس الکتریکی در یک محیط گاز خنثی به وجود می آید. در روش جوشکاری پلاسما، قوس الکتریکی حاصل از گازهای خنثی، دارای پلاسمایی با درجه حرارت بالا (حدود °C20000) می باشند که انرژی متمرکز بالاتر و قوس الکتریکی پایدارتری نسبت به روش TIG به دست میدهد.
الف) ویژگی های جوش پلاسما
جوش پلاسما دارای ویژگیهای زیر میباشد:
– جوش با کیفیت بالا به علت انرژی متمرکز بالا
– منطقه HAZ باریک
– محدود بودن تغییر شکل ها وتنش های پسماند
– عمق جوش به مراتب بزرگتر از پهنای جوش
ب) الکترود جوش پلاسما
الکترود غیر مصرفی از جنس تنگستن یا ترکیبی از آلیاژهای آن با توریوم است. الکترود جهت به حداقل رساندن استهلاک به قطب منفی وصل میشود.
پ) منبع تغذیه جوش پلاسما
جوشکاری پلاسما با جریان مستقیم صورت گرفته و منبع جریان آن عمدتاً یکسوسازها با مشخصه ولت- آمپر از نوع سراشیبی تند است.
ت) کاربرد جوش پلاسما
از کاربردهای جوش پلاسما میتوان به موارد زیر اشاره کرد.
– جوشکاری پلاسما عمدتاً برای جوشکاری انواع فولادهای زنگ نزن وفلزات غیرآهنی به کار میرود.
– کاربرد آن عمدتاً شبیه کاربرد روش TIG است. ولی ضخامت های نازک تر وضخیم تر را شامل میشود.
– جوشکاری قطعات ضخیم تا حدود ۵۰ میلیمتر، بدون استفاده از پخ زدن و بدون نیاز به الکترود مصرفی میباشد.
ث) تقسیم بندی روش پلاسما
روش پلاسما را با توجه به ضخامت قطعه کار میتوان در سه دسته زیر قرار داد.
– پلاسمای ظریف (میکروپلاسما) mm1-02/0 =t
– پلاسمای متوسط mm 3- 2/0 =t
– پلاسمای ضخیم mm 2 > t
ج) مزیت ها
از آنجا که این فرآیند بیشتر با فرآیند GTAW مقایسه میشود، مزیت های آن نسبت به GTAW عبارتند از:
– تمرکز انرژی بیشتر است.
– پایداری قوس مخصوص در جریانهای پایین، بیشتر است.
– گرمای تولیدی بیشتر است.
– جریان کمتری مورد نیاز است.
– حساسیت کمی نسبت به تغییرات طول قوس وجود دارد.
– آلودگی الکترود تنگستن محدودتر می باشد.
– به مهارت جوشکاری کمتری در حالت دستی نیاز دارد.
– گرمای ورودی کم، سبب کاهش پیچش میشود.
– برای نفوذ کامل به پشتی نیاز ندارد، زیرا از تکنیک سوراخ کلید استفاده میشود.
چ) محدودیت ها
محدودیتهای عمده پلاسما در مقایسه با GTAW عبارتند از:
– قیمت بالای تجهیزات (۲ تا ۵ برابر)
– نیاز به دانش بیشتر در زمینه جوشکاری
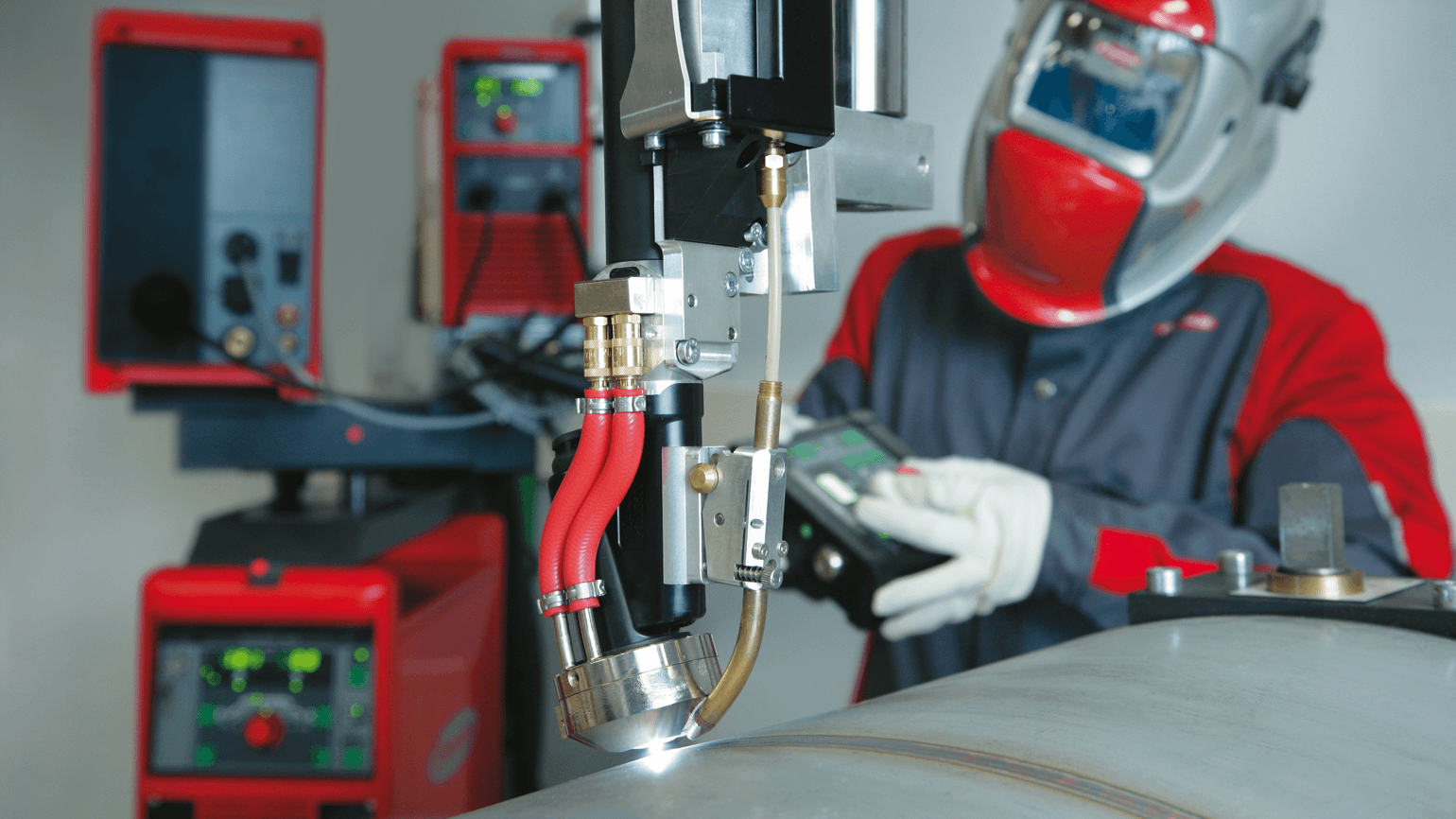
جوشکاری پلاسما-جوشکاری زائده ای- جوشکاریFCAW
۲- جوشکاری FCAW
فرآیند FCAW یک فرآیند جوشکاری قوسی است که در آن قوسی بین الکترود پیوسته فلزی و حوضچه جوش ایجاد میشود. این فرآیند بهوسیله گاز محافظ که از روانکاری درون الکترود لولهای شکل بدست آمده است و یا بدون محافظت اضافی، از طریق منبع تأمین گاز خارجی و بدون کابرد فشار انجام میشود.
دو نوع متفاوت از این فرآیند وجود دارد. در نوع اول علاوه بر روانکار موجود در هسته الکترود، از منبع گاز محافظ خارجی، جهت محافظت حوضچه جوش استفاده شده و در نوع دوم فقط به گاز محافظ تولید شده از تجزیه روانکار در درون الکترود تکیه میشود. این فرآیند جوشکاری در AWS نیز به دو فرآیند بدون استفاده از گاز محافظ (خود محافظFCAW-S ) و استفاده از گاز محافظ ( محافظ گازیFCAW-G ) تقسیم می شود. معمولاً فرآیند FCAW را جوشکاری سیمی خود محافظ و با مغزه گداز آور می شناسند. جوشکاری FCAW تقریباً همان جوشکاری GMAW است، با این تفاوت که نوع الکترود در آن متفاوت است. فرایند FCAW در سال ۱۹۵۰ و در ادامه فرآیند GMAW شناخته شد.
فرآیند FCAW از گرمای قوس ایجاد شده بین الکترود مصرفی تغذیه شونده که در هستهاش روانکار تعبیه شده است و قطعه کار، استفاده میکند. گرمای قوس، سطح فلز پایه و انتهای الکترود را ذوب میکند. محافظت اضافی از طریق احاطه حوضچه جوش، بوسیله منبع گازی ایجاد شده که با استفاده از یک نازل به سطح جوش دمیده میشود. ذرات درون الکـترود، گازی برای محافظت تولید میکنند. این ذرات نقشهایی نظیر اکسیژن زدایی، یونیزه کردن و زدودن آلودگیها را نیز بر عهده دارند و در برخی موارد عناصر آلیاژی را وارد جوش میکنند. ذرات روانکار از فلز جوش سبکترند، در نتیجه روی سطح جوش شناور شده و به عنوان یک پوشش محافظ عمل میکنند. الکترود به طور اتوماتیک از یک کلاف تغذیه میشود. قوس به طور اتوماتیک نگهداری شده و تولید به صورت دستی یا ماشینی صورت میگیرد.
الف) کاربرد فرآیند FCAW
توسط فرآیند FCAW میتوان فلزات آهنی و آلیاژهای دارای پایه نیکل، تمام فولادهای کم کربن وکربن متوسط، بعضی از فولادهای کم آلیاژی و فولادهای زنگ نزن را جوشکاری کرد.
به خاطر نفوذ عالی فرآیند FCAW میتوان از زوایه شیار°۳۰ استفاده نمود که منجر به صرفه جویی ۵۰ درصدی در مصرف فلز پر کننده، نسبت به فرآیند SMAW می شود. فرآیند SMAW نیازمند زوایای شیاری بزرگتر است. در بعضی موارد می توان از پخکاری اتصال در فلزات تا ضخامت ۱۳ میلمتر اجتناب کرد.
در این فرآیند، جوشکار بهترین کنترل را روی حوضچه جوش، نسبت به فرآیندGMAW دارد زیرا نیازی به نازل وپخش کن گاز نیست.
این فرآیند برای جوشکاری روی بویلرها، مخازن تحت فشار و فولاد ساختمانی مناسب میباشد. اکسیدکنندهها و عوامل فلاکس ساز موجود در الکترودهای این فرآیند، جوشهای مطلوبی را روی فلزات دارای سطح اکسیدی فراهم میکند. اغلب فلزات برشکاری شده با مشعل را میتوان بدون آمادهسازی قبلی جوشکاری نمود که سبب صرفه جویی درهزینهها میشود.
درشرایط محیطی با وجود وزش باد شدید، الکترودهای فرآیند FCAW، که به صورت خود محافظ میباشند، بهتر از الکترودهای فرآیند GMAW دارای حفاظ گازی، هستند.
ب) مزایای فرآیند
از مزایای این فرآیند میتوان به موارد زیر اشاره کرد:
– کیفیت بالای فلز جوش ته نشین شده
– ظاهر جوش مطلوب به خاطر صافی سطح جوش و یکنواختی آن
– خط جوش مطلوب برای جوشهای نواری افقی
– در گسترۀ بالایی از ضخامت، انواع فولادها را جوش میدهد.
– براحتی مکانیزه میشود.
– بهرهوری بالا از فلز جوش
– نسبتاً سریع است.
– قوس مرئی ایجاد میکند.
– نیاز به تمیزکاری سطح کمتری نسبت به GMAW دارد.
– پیچش کمتری نسبت به SMAW ایجاد میکند.
پ) معایب فرآیند
معایب این فرآیند عبارتند از:
– فقط برای فولادها به کار میرود.
– سیم الکترود آن گران است.
– تجهیزات آن نسبت به GMAW پیچیده تر و گران تر است.
ت) الکترود فرآیند FCAW
ساختار و ترکیب شیمیایی سیم جوش در این فرآیند، معرف تفاوت میان فرآیندهای GTAW و FCAW است. الکترود این فرآیند برخلاف فرآیند GTAW از یک لوله فلزی مجزا و نازک تشکیل شده است که با فلاکس پر شده ولی توپر نیست. فلاکس پودری مواردی نظیر عناصر آلیاژی، پایدار سازهای قوس، نیتروژن زداها، اکسیژن گیرها، سرباره سازها و مواد شیمیایی مولد گاز محافظ را تأمین میکند.
انواع الکترودهای توپودری براساس ترکیب پودر پرشده عبارتند از:
– الکترودهای تو پودری که خود تولید گاز محافظ کرده ونیاز به گاز محافظ ندارند.
– الکترودهای تو پودری که نیاز به گاز محافظ دارند.
سرباره تولید شده، از حوضچه جوش در برابر اکسیژن و نیتروژن هوا محافظت کرده و باعث کند شدن سرعت سرد شدن و همچنین تا حدودی مانع تشکیل مارتنزیت میشود. در این فرآیند براساس نوع الکترود مورد نیاز پولاریتههای DCEP و DCEN استفاده شده و از جریان AC استفاده نمیشود.
الکترود مصرفی در جوشکاریFCAW دارای قطر ۴-۸/۰ میلیمتر است. این الکترود معمولاً بصورت کویل و قرقره در بازار موجود میباشد.
۳- جوشکاری زائده ای
به طور کلی به اتصال زائده فلزی (میلهای شکل یا شبیه آن) به سطح قطعه کار جوشکاری زائدهای گفته میشود. این فرآیند نوعی جوشـکاری قوسی است که در آن انتهـای زائده و سطح قطعه کار، بهوسیله قوس ایجاد شده بین آنها، گرم و ذوب میشوند. در اثر فشار وارد شده بر زائده، در لحظه معین قوس قطع شده و زائده به درون حوضچه مذاب در روی سطح کار، فرو رفته و پس از انجماد به آن متصل میشود. دو روش عمده برای جوشکاری زائدهای وجود دارد.
۱- جوشکاری قوسی زائده ای
۲- جوشکاری تخلیه خازنی زائده ای
در هر دو روش از جریان مستقیم و قوس استفاده میشود. توان مورد نیاز توسط موتور ژنراتور، مبدل یکسو کننده یا باطری ذخیره، تأمین میشود. برای روش تخلیه خازنی، نیاز به سیستم ذخیره الکترود استاتیک با ولتاژ پایین است و قوس با تخلیه سریع انرژی الکتریکی ایجاد میشود. کنترل کننده جریان، کنترل کننده زمان جوشکاری، کابلهای اتصال و تفنگی، تجهیزات تکمیل کننده هر دو روش هستند. مشعل تفنگی وظیفه نگهداشتن زائده و هدایت دقیق آن به طرف محل اتصال را به عهده دارد. در روش قوسی معمولاً از یک حلقه سرامیکی استفاده میشود. این حلقه سرامیکی که بر روی زائده قرار گرفته و بر روی تفنگی نصب میشود، اعمال زیر را انجام میدهد.
- تمرکز حرارت قوس درموضع معین بر روی کار
- ممانعت از نفوذ جریان هوا به موضع جوش و جلوگیری از اکسید شدن فلز مذاب
- جلوگیری از جاری شدن و پخش شدن ذرات مذاب
- محافظت جوشکار از نور قوس ایجاد شده
در هر دو روش، زائده نقش الـکترود را داشته و تفنگـی به عنـوان نگهـدارند الکترود میباشد. زمان قوس در روش تخلیه خازنی به قدری کوتاه است که نیازی به حلقه سرامیکی نیست. در جوشکاری آلیاژهای آلومینیوم به روش قوسی زائدهای، نیاز به گاز محافظ میباشد، در صورتی که در روش تخلیه خازنی نیازی به این گاز نیست. در جوشکاری آلیاژهای آهنی به روش قوسی، معمولاً از پلاریته DCEN استفاده میشود و پلاریته DCEPبرای فلزات غیر آهنی مورد استفاده قرار میگیرد.
جوشکاری زائدهای فرآیندی سریع محسوب میشود. زمان جوش به نوع روش و قطر زائده بستگی دارد. این زمان برای روش تخلیه خازنی از ۶ تا ۱۰ میلی ثانیه و برای روش قوسی از ۱/۰ ثانیه تا کمی بیشتر از ۱ ثانیه میباشد. جوشکاری زائدهای در بیشتر موارد، نیاز به سوراخکاری را که معمولا برای اتصـال زائدهها از طریق پیچ انجام میشود، بر طرف نموده است. زائدهها مـیتوانند در شکـلها و اندازههای مختلف ساخته شوند و معمولا از جنس آلیاژهای آهن کم کربن، فولادهای زنگ نزن و آلومینیوم میباشند.
انواع فولادها، آلیاژهای آلومینیوم، برخی ازآلیاژهای مس، آلیاژهای زیرکونیوم، منیزیم، تیتانیوم و آلیاژهای روی که با روش دایکاست تولید شدهاند، با این فرآیند جوشکاری میشوند. روش تخلیه خازنی امکان اتصال فلزات غیر هم جنس را نیز فراهم میسازد. روش قوسی محدودتر است و بیشتر برای فولادها و آلومینیوم بکار میرود. روش تخلیه خازنی به سه روش دستهبندی میشود که عبارتند از:
- تماس اولیه
- فاصله اولیه
- کشش قوس
الف) کاربرد روش جوشکاری زائدهای
روش جوشکاری زائدهای در صنایع مختلف از جمله کشتی سازی، هواپیما سازی، صنایع الکتریکی و … بهکار میرود.
ب)مزایا جوشکاری زائده ای
مزایای جوشکاری زائدهای عبارتند از:
– عدم نیاز به سوراخکاری و پیچ کردن برای نصب زائده
– سرعت بالای کار
– عدم نیاز به دو سطح قطعه کار
– پیچیدگی ناچیز به علت کم بودن زمان قوس
پ) محدودیتهای جوشکاری زائدهای
موارد زیر از محدودیتهای جوشکاری زائدهای میباشند.
– اندازه و قطر زاده برای ورقهای نازک محدود است.
– امکان اتصال زائده دو طرفه بسیار کم است.
– کاربرد آن برای فلزات غیر آهنی محدود است و به تکنیک ها و تجهیزات ویژه ای نیاز دارد.
نظرات